From boats to drones, the propeller has been a similar design since the beginning, but innovative toroid propeller designs have been demonstrated to increase efficiency or reduce noise. Two independent teams have furthered the design of toroid propellers – one for drones and flights and another for propellers in boating where they have demonstrated 105% performance improvement under certain conditions.
The torus marine propeller, then described as one featuring “double blades”, was invented in the early 1890s by Charles Myers from Manchester, and refined over time. Wikipedia reports that this class of patents features over 150 patents in 120 years worldwide as of 2022. The design distributes vortices generated by the propeller along the entire shape of the propeller, which means that noise is distributed and dampened more quickly.
In the same way that we see continuing improvements in electric motors, it is possible that propeller design will also provide new solutions.
Drone Sound Annoying
The buzzing sound is caused by the propeller tip speed at 100 Hz to 5kHz which is the sound of a baby crying or a wasp. Removing that sound makes drones more acceptable. Whereas the design for shipping is all about efficiency.
The tip speed of a 10m propeller on a ship at 100 rpm on a cargo ship is similar to the tip speed of a small prop at much higher speeds.
How the New Innovative Toroid Propeller Design Works
Two independent labs came up with a revised Toroid design. The MIT Lincoln Laboratory and US-based company Sharrow Marine took the two most challenging features of traditional rotors– their whining buzz and outdated efficiency — to propose twisted, toroid-shaped propellers that dramatically reduce noise while maximizing performance without energy waste.
Each designed its models slightly differently The quiet toroidal propeller consists of two blades looping together so that the tip of one blade curves back into the other. This closed-form structure reduces and controls the drag effects of swirling air tunnels (i.e., vortices) created at the blades’ tips and strengthens the propeller’s overall stiffness. As such, the propeller’s acoustic signature is significantly decreased without affecting its performance.
MIT Lincoln Lab
Dr Thomas Sebastian (press release here) and their publication here explains their innovation. The toroidal propeller, one of the Lab’s @RD100Awards winners, has a unique, closed-form propeller design that makes it a significantly quieter alternative to common multirotor propellers on commercial uncrewed aerial vehicles.
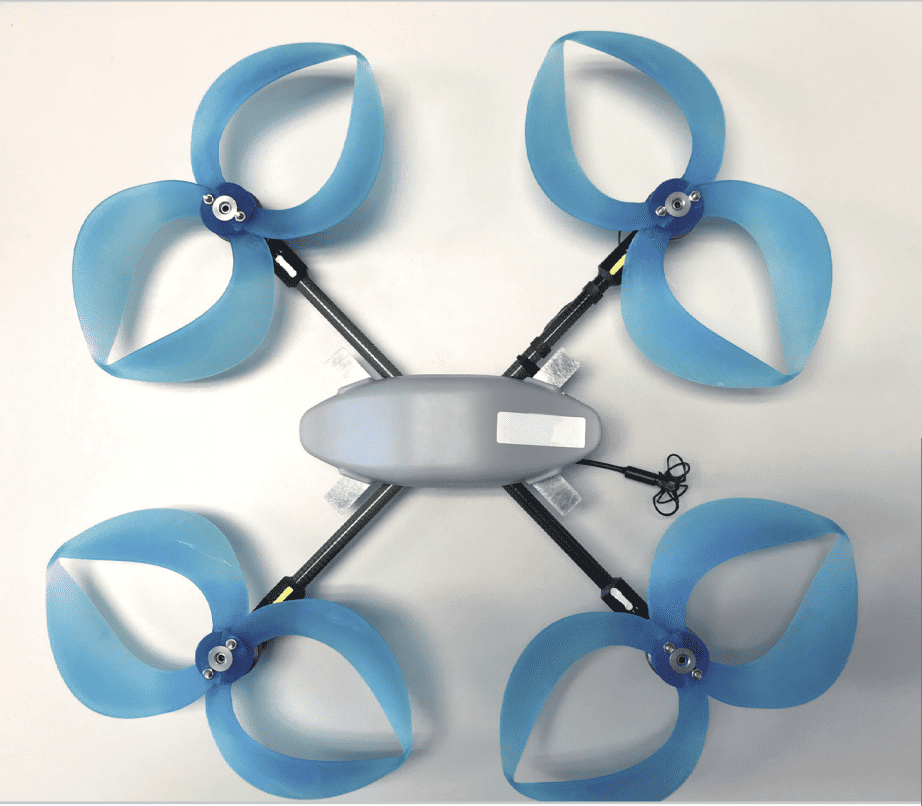
Sharrow Marine for Boats
Independently, Cheryl Main of Sparrow Marine came up with a toroidal propeller for boats (see their website here) with 5 blade design.
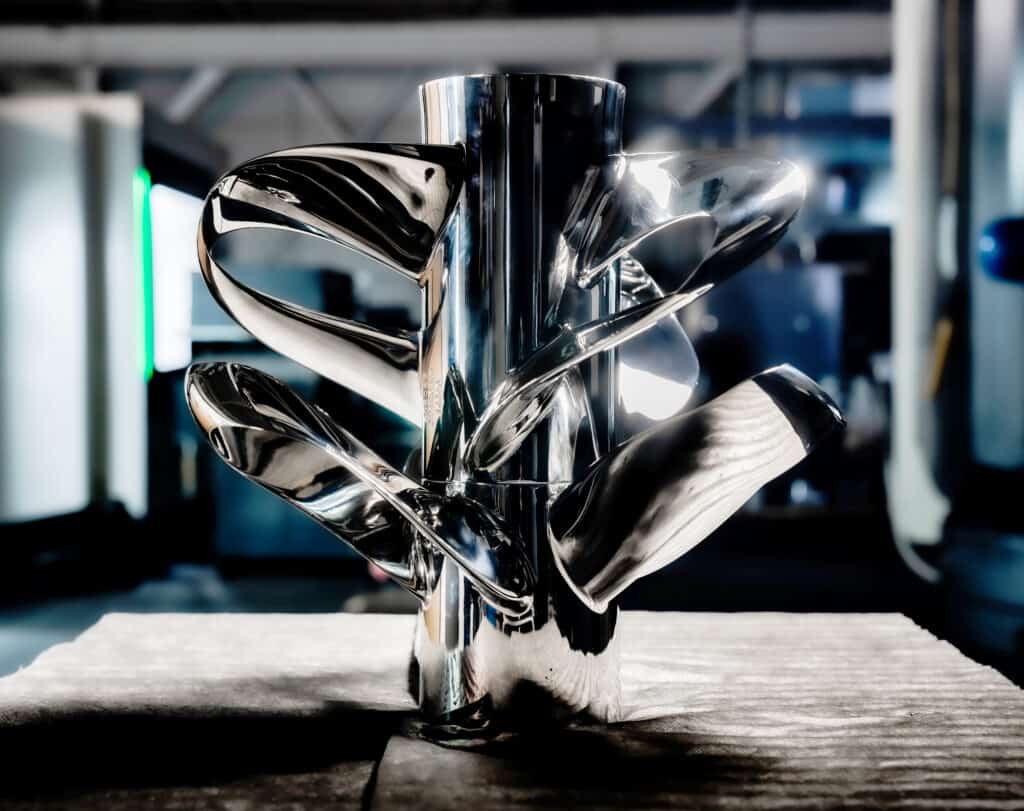
The design reduces cavitation. The propeller can increase range by 30%, drive the propeller at 1000 rpm lower, and 30% more efficient.
Implications for Efficiency
Electric Planes and VTOL
Electric planes are already here. Emissions are 2.5% to 3.5%. Increasing efficiency by 30% extends the range, and lowers cost of transportation. Have airplane designers looked at improving design? Possibly, but more likely with dozens of problems to solve designers work within existing technology and parameters. Almost certainly enhancements in lift or noise will become limiting at some stage and this approach may solve some of their issues – either efficiency or noise.
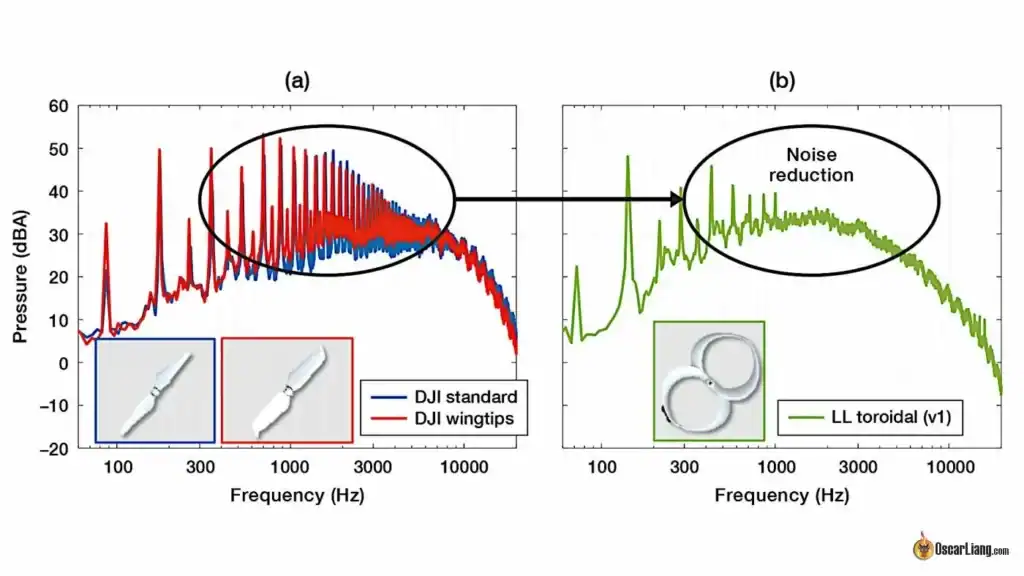
Boats
Marine tonnage is 3% of global emissions. While changing to renewable energy will reduce shipping by 50%, a further improvement in efficiency will enable more cargo ships to use electric propulsion extending their range.
For smaller craft, this result shows a 105% improvement in prop efficiency at 4,000 rpm. The prop enabled faster acceleration from 14sec to 10 secs from 1 to 30 mph. Adoption of more efficient motors may be of little interest to recreational boaties, but might be to other sectors or electric engine manufacturers.
In one study, fuel savings were about $2 per nautical mile. ($194 for 100 nm).
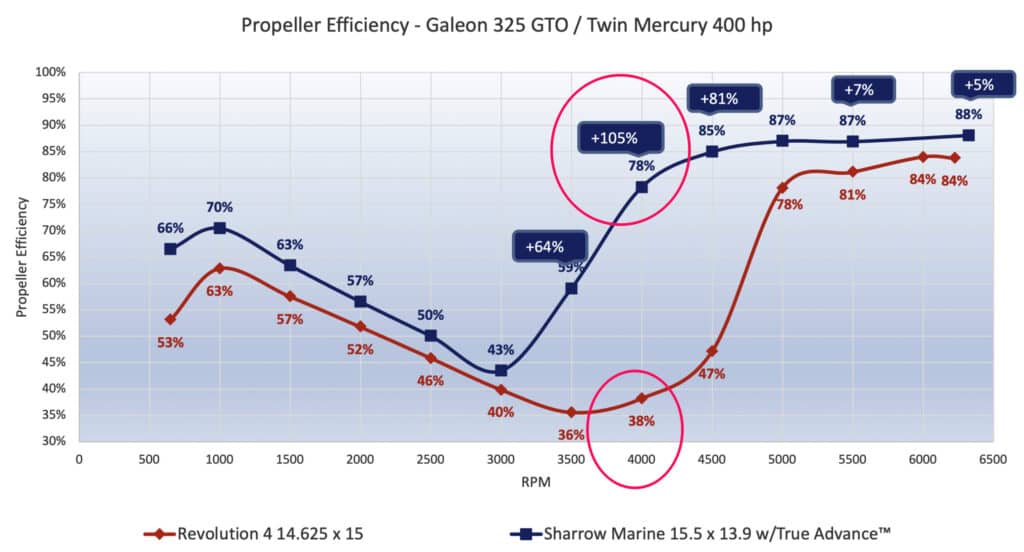
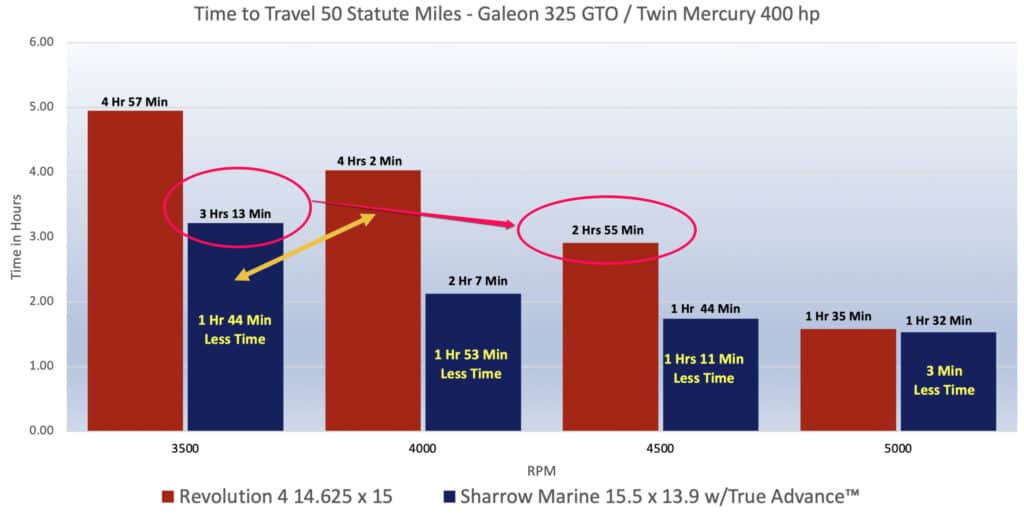
Challenges and Market Introduction
Innovation can be understood in the context of 5 orders of innovation as per this post. This is a order 4 innovation so there is no change needed in underlying business of flying or shipping. This just increases efficiency. Sharrow have priced their propeller at 10X the cost of existing propellers. But 30% reduction in fuel costs is an enormous return on investment. It would make electric boats even more cost-effective. And for drones, removing the annoyance factor could change from no go to acceptable
The challenge is manufacturing at scale. Currently, either 3d printed or machines Toroid design shows there is scope for further improvements.
More Reading
This innovation has been widely reported
https://www.ll.mit.edu/doc/toroidal-propeller
https://oscarliang.com/toroidal-propellers/
https://en.wikipedia.org/wiki/Toroidal_propeller
Matt from the Youtube channel Undecided with Matt Ferrell on this a well worth viewing summary https://youtu.be/UzYHO4tksTc and on his website here
Contrarian View from Commentator
A commentator (https://www.youtube.com/channel/UCkHpTLHcub_eA8H0Rjtp_rg has a different perspective. Their comment is about fixed pitch propellers for aircraft. Their highest efficiency occurs when the forward movement matches that of the prop’s pitch relative to the RPM setting. Remember a prop is a screw. If the forward movement of the screw does not match that of the pitch/RPM, it is an inefficient use of energy. Accordingly, it’s not that this new design is so amazing efficient. It’s that fixed pitch props are so amazingly inefficient at all RPM settings outside of their ideal pitch/movement. Accordingly, 105% is easily believable and likely very accurate.
That said, contrary to the video’s false assertions, this technology likely has little use outside of tri/quads and small boats. As props get larger and larger they are intended to spin much more slowly, if for no other reason than to avoid super sonic tip speeds (example, helicopters and cargo ships). The larger the prop the less likely they are to have high RPM requirements. Which is in large part why the prop blades become wider. In other words, they get their performance from size, not speed (RPM).
Relevance in Cargo Ships
This also means the operating RPM window is drastically reduced 1500-6000 RPMs (4500 rpm window) vs for example, 100-250 RPM (150 rpm window), of a large cargo ship). This in turn means a large ship’s propeller is much more likely to always operate at or near ideal RPM whereas the smaller boats commonly transition to and fro as their standard operating environments. Accordingly, inefficiency is much more commonly observed. In turn making the efficiency improvements a much larger percentage of it’s overall fuel consumption as it commonly spends more time as it transitions in the less ideal RPM range.
For example, a small craft likely operates around 20% of it’s life in transition. Whereas a large ship likely operates 0.0001% of it’s life in transition, with a much smaller window for transition. Accordingly, a well-optimized fixed pitch is almost always be ideal for large cargo ships. Additionally, for things like wind turbines, most prop aircraft, and so on, they already have variable pitch props, which addresses this inefficiency.